A big congratulations to our Kyrgyzstan client on the smooth delivery of their tailored bread and hamburger production line, which is just an important milestone in their production upgrade journey! This client approached Gondor Machinery with a clear goal: to build a fully customized, integrated, and efficient production line that could support the large-scale manufacturing of diverse food products while ensuring product standardization, hygiene, and long-term operational stability.
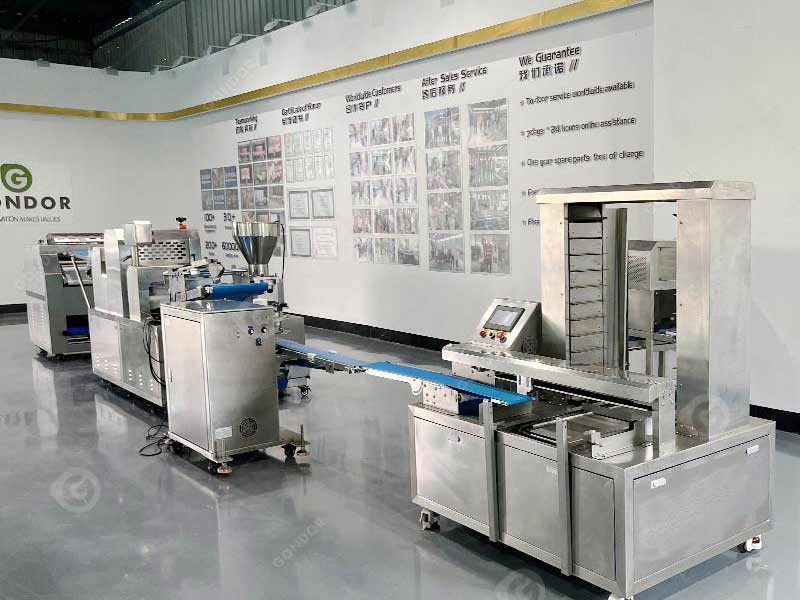
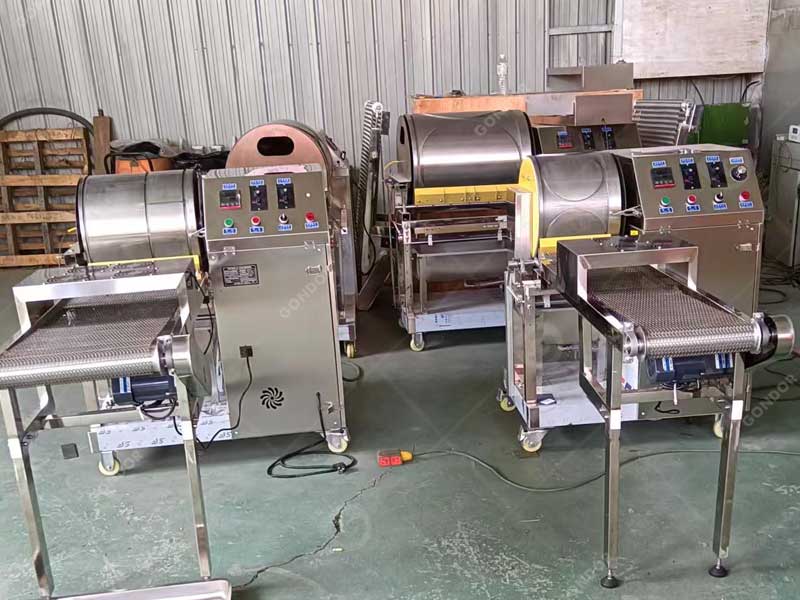
Project Snapshot: Tailored Bakery and Burger Line for Kyrgyzstan Client
On March 20, 2025, a mid-sized food manufacturing company from Kyrgyzstan reached out to Gondor Machinery via our official website. The company was facing rapid business growth, which is driven by rising demand for its core products, including hamburgers, sandwich buns, stuffed bread, steamed buns, and crepes. However, their production processes were still largely dependent on manual and semi-automated methods, which will lead to low productivity, inconsistent quality, and high labor dependency.
After carefully reviewing the client’s production challenges and long-term goals, our team proposed a fully customized production solution tailored to their specific needs. Through a series of detailed consultations and technical assessments, our technical team designed an integrated system that combined five essential machines: a complete bread production line, a hamburger patty forming machine, a battering machine, a breading machine, and a spring roll wrapper making machine.
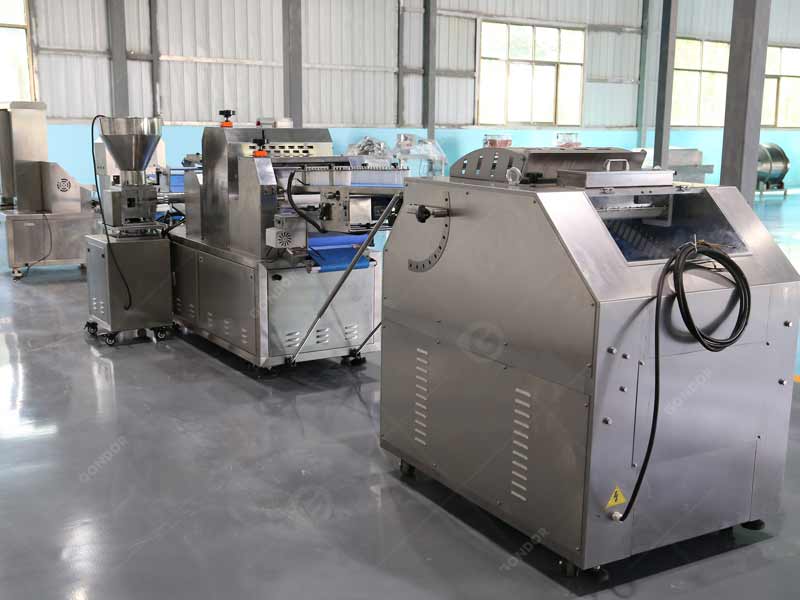
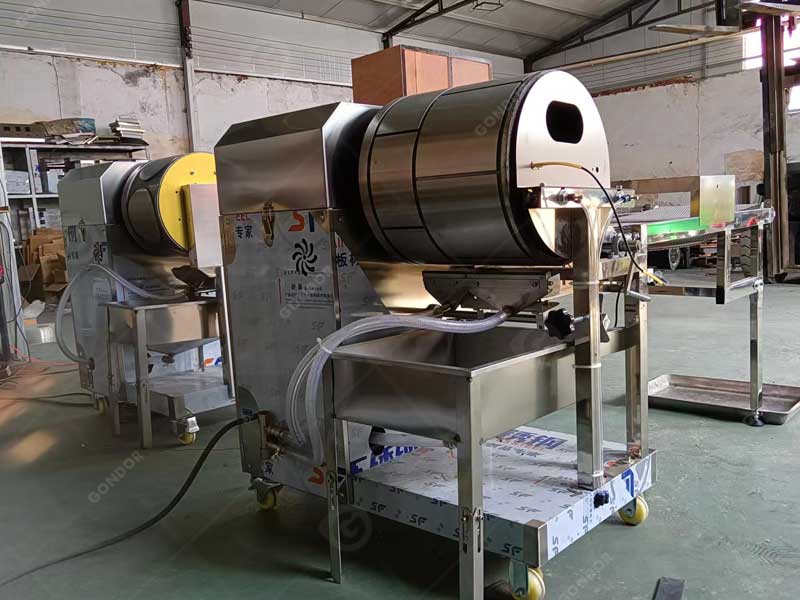
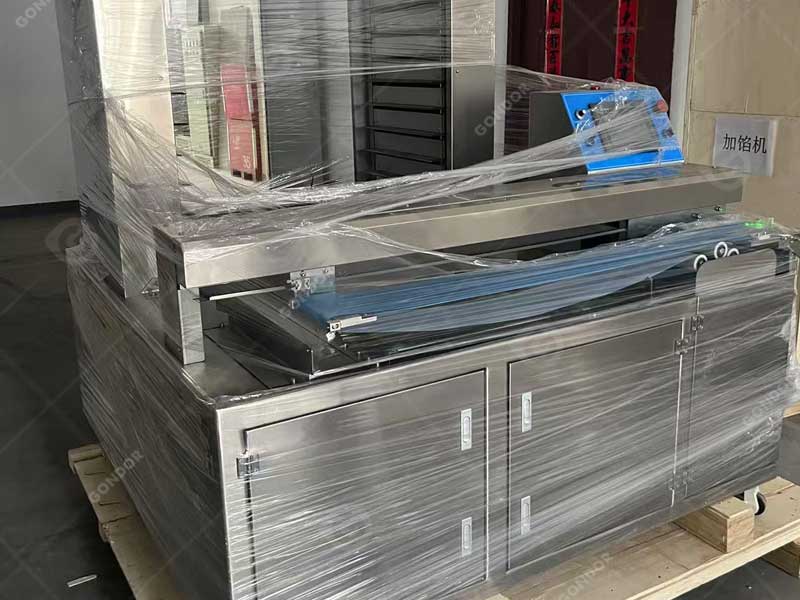
Customer Focus: Multifunctional, Easy-to-Use, and Stable Solutions
After communication, we learned that the client’s original production facility was typical of many growing manufacturers in emerging markets: limited automation, high reliance on skilled workers, and time-consuming manual operations. As the customer base grew, including restaurants, school canteens, and distributors, the client was struggling to meet order volume while maintaining consistent product quality. Therefore, the client placed particular emphasis on the following aspects during this equipment purchase:
- The equipment should support flexible switching between multiple product types (such as burger buns, steamed buns, crepes, etc.).
- The user interface should be intuitive,which allows for short training periods and easy operation.
- The equipment should have a robust structure, operate reliably, and be easy to maintain.
- The supplier should provide sufficient spare parts and responsive after-sales support.
- A live on-site trial run before placing the order was required to ensure the equipment met expectations.
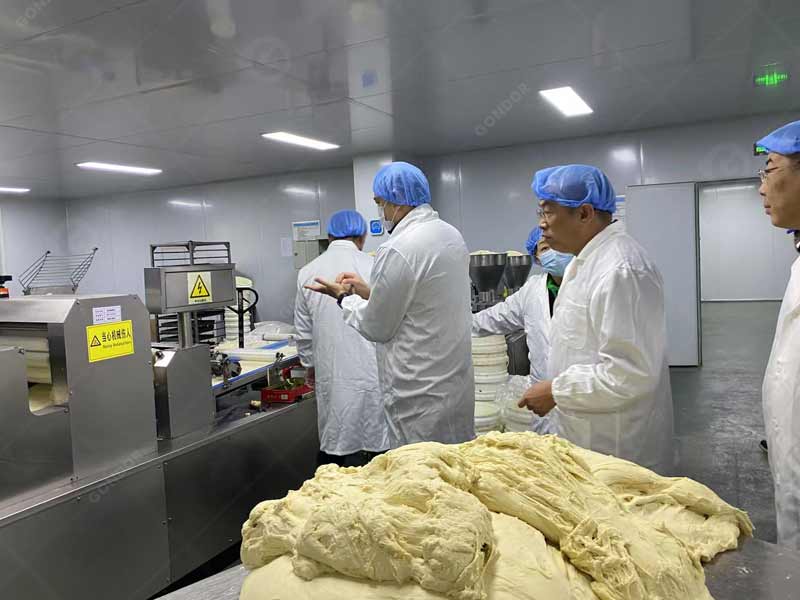
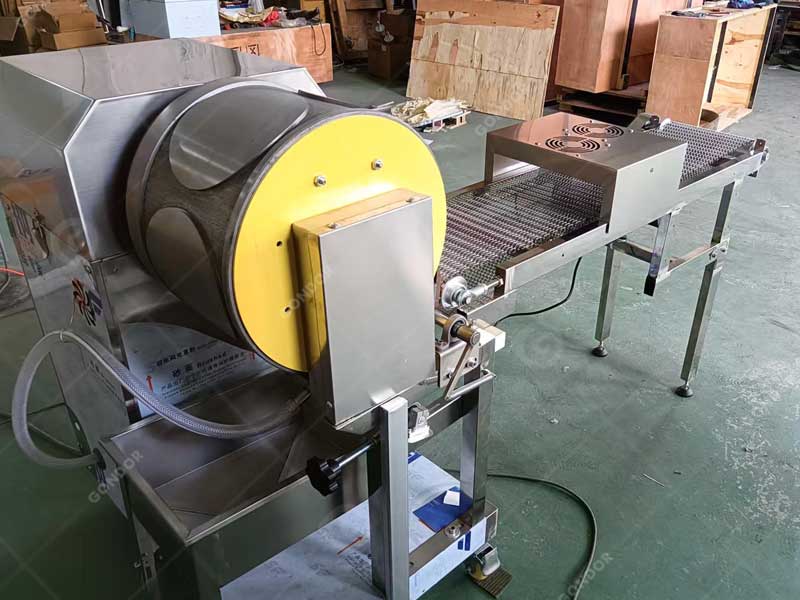
Gondor Custom Solution: Precisely Meets Client Needs
To meet the client’s specific business goals, our engineering team designed a modular, high-efficiency production line capable of producing several food categories on the same system. Each machine was selected and configured to match the client’s product types, volume expectations, and available plant space.
- Dough mixer with variable speed settings and high-capacity mixing blades
- Dough divider and rounder for precise portioning and uniform shaping
- Intermediate proofer that maintains optimal temperature and humidity
- Moulding and flattening units for forming burger buns or sandwich loaves
- Convection oven with multiple baking zones and intelligent temperature control
- Cooling conveyors and collecting system for post-baking handling
- Consistent patty size and weight, reducing product variation
- Quick-change molds for different patty sizes
- Easy disassembly for cleaning and sanitation
- Continuous-flow battering with adjustable viscosity and coating thickness
- Breading unit with upper and lower crumb applications for full coverage
- Integrated conveyor with speed and vibration control
- Easy wash-down features for daily sanitation
- Producing thin, evenly cooked wrappers at high speed
- Customizable wrapper sizes and thickness
- Easy integration with batter dispensers or filling stations in the future
Seamless Project Execution: From Quote to Commissioning
One of our core strengths is efficient project delivery. In this case, the client first contacted us on March 20, 2025, and confirmed their order just nine days later on March 29. This rapid turnaround was made possible by the close coordination between our sales engineers and the client, supported by clear documentation and a well-defined production schedule. During the manufacturing phase, the client made two visits to our factory in Luohe City, and our office in Zhengzhou City, Henan Province, China. Our team prepared live trials using the client’s preferred ingredients. These sessions allowed them to observe:
- Dough texture and proofing performance
- Bun shaping and baking consistency
- Patty shape, weight accuracy, and cooking texture
- Coating uniformity in the breading system
- Spring roll wrapper thickness and flexibility
Proven Results and a Growing Partnership
Following the deployment of Gondor’s customized equipment, the client experienced clear, measurable improvements in production efficiency and product quality. This successful implementation not only resolved immediate operational challenges but also laid the foundation for future growth and collaboration.
- 60% increase in daily output, enabling faster fulfillment of bulk orders
- Enhanced product consistency, particularly in bun size and crust color
- Lower operating costs through reduced dependence on skilled labor
- Minimized production waste due to precise portioning and shaping
- Faster product changeovers enabled by programmable controls and easy-clean features
- Labor reallocation to packaging and logistics without increasing headcount
- Scalable, high-output production system for multiple product categories
- Transparent procurement process with live testing and clear technical specifications
- Comprehensive support including installation, training, and spare parts supply
- Flexible solution designed to support future product line expansion
Conclusion: Tailored Automation is the Future of Food Processing
This successful project in Kyrgyzstan demonstrates that customized automation is essential for food processing equipment manufacturers aiming to improve efficiency, ensure consistent quality, and support long-term business growth. By delivering a fully integrated bread and hamburger production line, Gondor Machinery helped our client shift from manual workflows to a streamlined and scalable system.
If you are planning to upgrade your current production or launch a new food processing line, this is the right time to explore customized solutions. And Gondor Machinery is ready to be your trusted partner in building a smarter, more efficient future for your factory. Contact us today to discuss your project demands!